How serial Flash technology is evolving to meet the new requirements of Industry 4.0 designs
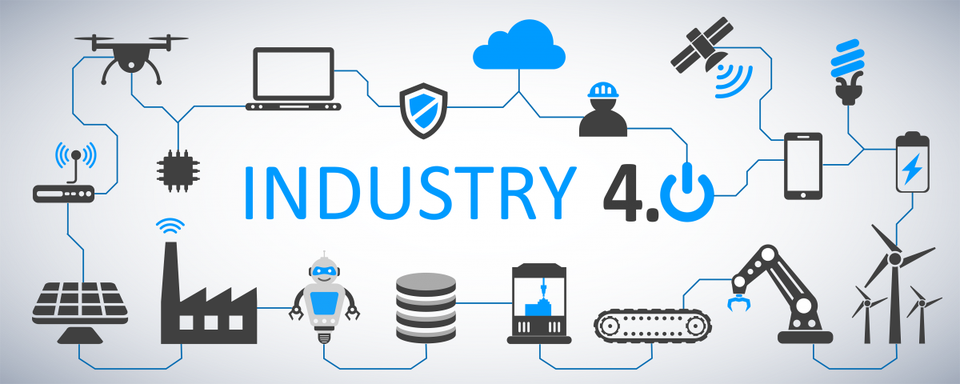
The famous fourth industrial revolution, tagged ‘Industry 4.0’, is based on the move to digitize industrial equipment and processes on a massive scale. This Industry 4.0 trend is now stretching the capabilities of almost every important category of electronic component used in industrial machines and systems.
Non-volatile memory is no exception. Non-volatile memory is being challenged to meet new requirements in Industry 4.0 designs in five main ways:
- Cost
- Size
- Speed
- Power consumption
- Security
While various alternative non-volatile memory technologies continue to put up a challenge, it is proven, familiar Flash technology which is evolving fastest and most effectively to meet these new challenges. This article describes recent innovations in Flash memory products which will help system designers implement new equipment designs for Industry 4.0 applications.
The demands of Industry 4.0
Industry 4.0 is defined by business consultancy McKinsey as: ‘The next phase in the digitization of the manufacturing sector, driven by four disruptions: the astonishing rise in data volumes, computational power and connectivity, especially new low-power wide-area networks (LPWANs); the emergence of analytics and business intelligence capabilities; new forms of human-machine interaction such as touch interfaces and augmented reality (AR) systems; and improvements in transferring digital instructions to the physical world, such as advanced robotics and 3D printing.’
Industry 4.0 equipment is notable for its extensive generation and use of ‘big data’, facilitated by always-on, pervasive connectivity to the internet. As LPWANs proliferate in factories, warehouses and industrial campuses, the supply chain will increasingly be able to share real-time monitoring data about products, inventory and assets with sophisticated analytics software in the cloud.
Underpinning this explosion of digitization will be the massively increased deployment of sensing devices, such as RFID smart tags which can be read wirelessly. These devices, operating from a battery power supply or even from harvested energy, will often require an ultra-low power memory component for storing logged data.
A completely different challenge will be posed by new control technologies for industrial equipment. For all the hype around today’s testing of autonomous vehicles on public roads, it is in factories and warehouses, which stand to gain huge efficiency and safety benefits from the elimination of human drivers, that autonomous vehicles such as fork-lift trucks and motorized trolleys are being first deployed (see Figure 1).
Fig. 1: the autonomous Linde R-MATIC reach truck transports palletized goods of up to 1.6 tons fully automatically to high-bay racks. (Image credit: Linde)
Similarly, AR and virtual reality (VR) are best known as consumer technologies, but again offer huge potential value in the factory, for instance to assist in manual assembly, maintenance or repair operations.
New implementations of these sophisticated applications will run on vast application code bases, far greater than is typical for today’s industrial appliances. This will bring pressure on industrial system designers to find code storage solutions which meet the hugely increased capacity requirement without a similarly huge increase in bill-of-materials cost and board footprint.
Lastly, a common theme in all types of Industry 4.0 equipment is connectivity – and connectivity brings an inherent risk of compromised security. By guaranteeing the authenticity of the devices that store code and data in Industry 4.0 equipment, secure non-volatile memory chips can provide a hardware barrier to intrusion into sensitive industrial networks.
Evolution of Flash technology for the Industry 4.0 age
Over the years, various non-volatile memory technologies have made claim to superiority over Flash in one characteristic or another. But as the incumbent, pre-eminent technology for non-volatile storage, Flash has the advantages of being:
- Familiar
- Proven in tens of thousands of applications
- Available in large volumes in a very wide choice of product configurations, to give a flexible set of product options for the system designer to choose from
- Backed by the resources of the world’s leading memory IC manufacturers, including Winbond. These manufacturers continually invest in improvements to fundamental Flash fabrication technology, packaging, and device performance and features.
Now, Flash product manufacturers are responding quickly and effectively to meet the new memory requirements of manufacturers of Industry 4.0 equipment and systems, introducing new solutions optimized for cost, size, performance, power or security.
Packaging innovations
The semiconductor industry's favored method for achieving size and cost reduction is the process shrink. For the high-end microcontrollers used in Industry 4.0 equipment, this is true of the CPU circuitry. Many manufacturers of leading-edge MCUs today are looking to migrate designs from 4xnm nodes to 3xnm nodes to benefit from performance and cost improvements. At 3xnm nodes, however, the NOR Flash circuitry embedded in the MCU die actually becomes more expensive – shrinking NOR Flash beyond 4xnm nodes is proving to be problematic. But Winbond is innovating in partnership with MCU manufacturers to provide stacked die solutions, combining an MCU die fabricated in a 3xnm process with a 4xnm NOR Flash die in a single package, and providing the optimal combination of footprint, performance and code storage capacity for high-end industrial designs.
Power innovation
Wireless smart tags or labels are increasingly being used in industrial applications to provide real-time monitoring data, for instance to continually record the temperature and humidity conditions in which perishable goods or pharmaceuticals are kept when in transit. They require the capability to store potentially large amounts of logged data, but operate from extremely constrained battery power supplies, or even from harvested energy.
To support the use of very low-voltage battery or harvested power supplies, discrete Flash ICs are being developed which operate at a voltage below the standard 1.8V low-power level for external Flash ICs. For instance, Winbond supplies the W25QxxNE 1.2V and W25QxxND extended 1.5V SpiFlash NOR Flash parts in 8-pin packages (see Figure 2). The devices offer a maximum 52MB/s data transfer rate and support a standard, dual and quad Serial Peripheral Interface (SPI) and Quad Peripheral Interface (QPI).
Fig. 2: the Winbond 8Mbit 25Q80NEXIG 1.2V Flash IC in a 2mm x 3mm USON8 package. (Image credit: Winbond)
Performance innovation
SPI NOR and serial NAND Flash are core technologies in the industrial sector, providing compact, low pin-count solutions for code and data storage. But the conventional serial architecture of these devices can act as a limiting factor on the speed with which data can be read and written, producing a slower data transfer rate than equivalent parallel Flash parts.
Now Winbond is innovating with new high-performance serial NAND Flash technology. Single-level cell (SLC) NAND Flash provides a high-reliability data storage medium in industrial applications. But in applications which require a high data transfer rate, designers have traditionally used NOR Flash, which offers lower density and hence a higher cost-per-bit than NAND Flash, but higher speed.
Now Winbond has introduced the W25N01JW, a 1Gbit serial NAND Flash part which offers a maximum data transfer rate of 83MB/s - comparable with that of SPI NOR Flash devices. Even more impressively, the Winbond architecture supports an octo configuration - a two-chip dual quad serial interface which doubles the data transfer rate to a maximum of 166MB/s (see Figure 3).
This is sufficient to support demanding, data-rich graphics applications, providing a high-capacity, low-cost alternative to NOR Flash in densities of more than 512Mbits. Automotive-qualified, the W25N01JW is in development in vehicle instrument cluster systems, and is equally suitable for industrial autonomous vehicles and AR/VR applications.
Fig. 3: the dual quad architecture of the W25N01JW serial NAND Flash device. (Image credit: Winbond)
Security innovations
The pervasive connectivity of the Industry 4.0 world exposes equipment to risks from malicious actors intruding into networks, compromising users' privacy or stealing data. There are many measures available to designers to combat security risks. One important measure is hardware authentication, to guarantee that only authorized devices share data over a network.
To provide hardware authentication for critical software such as boot code, Winbond has introduced the W74M family of Authentication Flash Memory solutions. Each W74M part incorporates an SPI Flash memory with a security IC in a multi-chip module. The device is secured with a standard HMAC-SHA-256 crypto accelerator and four monotonic Flash counters which are HMAC-signed by individual secret keys. The W74M enables system designers to implement multi-layered authentication for code and data storage for devices on the network edge or outside the cloud.
Access to the code or data stored in the Authentication Flash memory is protected by a secure key, which is unique to each manufactured unit. In the event of tampering or intrusion into the network, the boot code or data stored on an Authentication Flash will remain secure from attempts to steal, modify or impair it.
Flash technology evolves to meet Industry 4.0 requirements
Non-volatile storage of code and data is one of many functional elements in industrial equipment, and as the Industry 4.0 trend towards ever greater digitization and data analytics gathers speed, the demand for higher non-volatile memory capacity, higher speed, lower power and lower cost will also intensify.
As this article has demonstrated, new product developments in the SPI NOR and serial Flash categories are helping to ensure that Flash technology retains its place as the favored non-volatile memory choice for designers of industrial equipment as they adapt to the Industry 4.0 era.